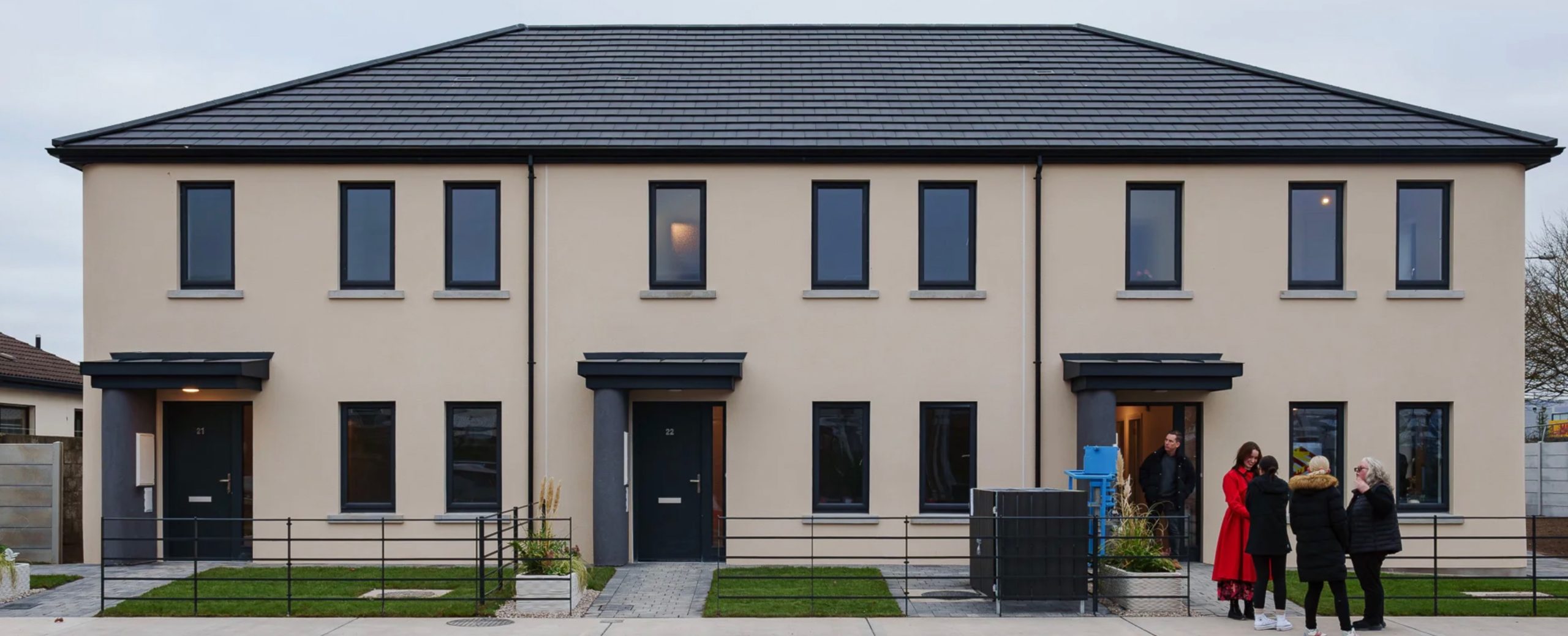
Ireland gets world’s first printed social houses - Global Construction Review
The world’s first printed concrete social housing project has gone up in Ireland – a terrace of three, 3-bedroom houses in Grange Close, Dundalk, County Louth.

Ireland gets world’s first printed social houses
Rod Sweet
17.12.24
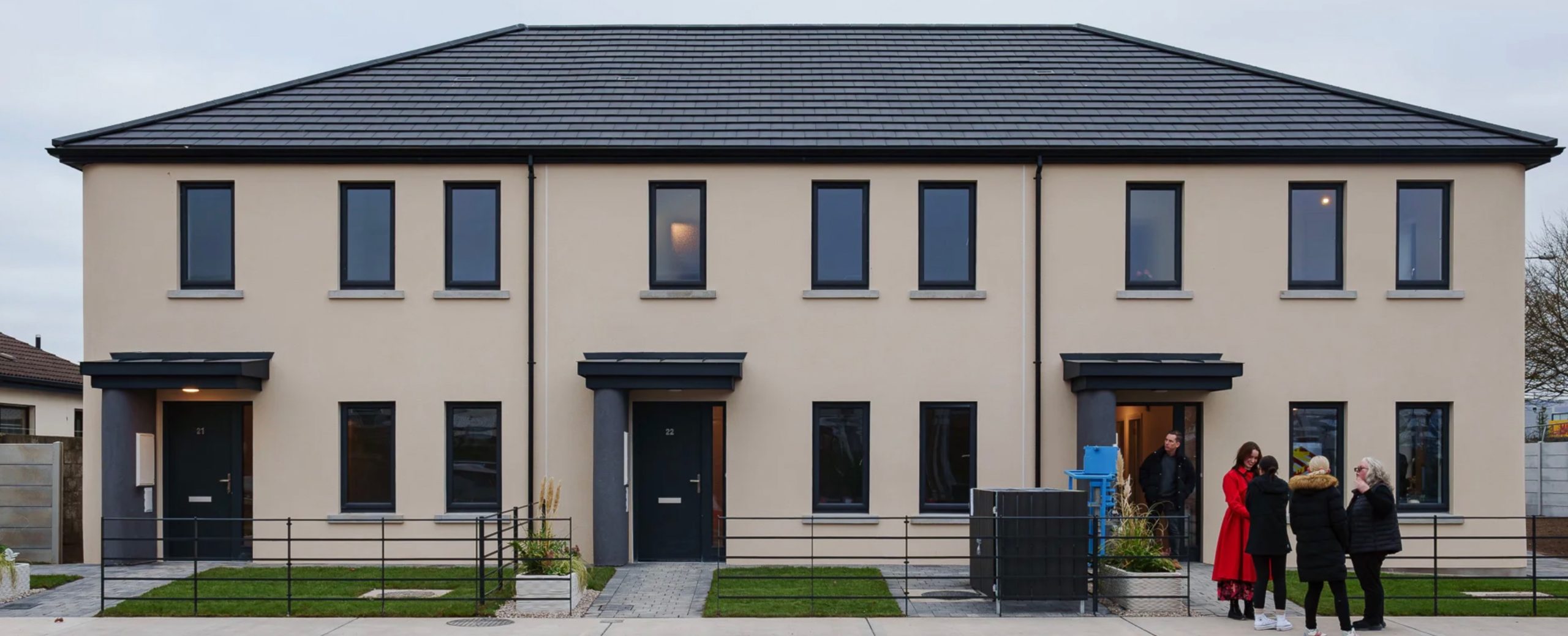
The world’s first printed concrete social housing project has gone up in Ireland – a terrace of three, 3-bedroom houses in Grange Close, Dundalk, County Louth.
The 330-sq-m development was a collaboration between Louth County Council, 3D print specialist Harcourt Technologies (HTL.tech), and building material company Roadstone.
Using a construction printer made by Danish manufacturer Cobod, crews finished the structure in 132 days from initial site preparation to key-handover.
Cobod said that was a 35% time reduction on the 203 days typically required using traditional construction methods.
The walls were printed in 12 days, including printer setup and takedown time. The entire structure was completed in 18 days, Cobod said.
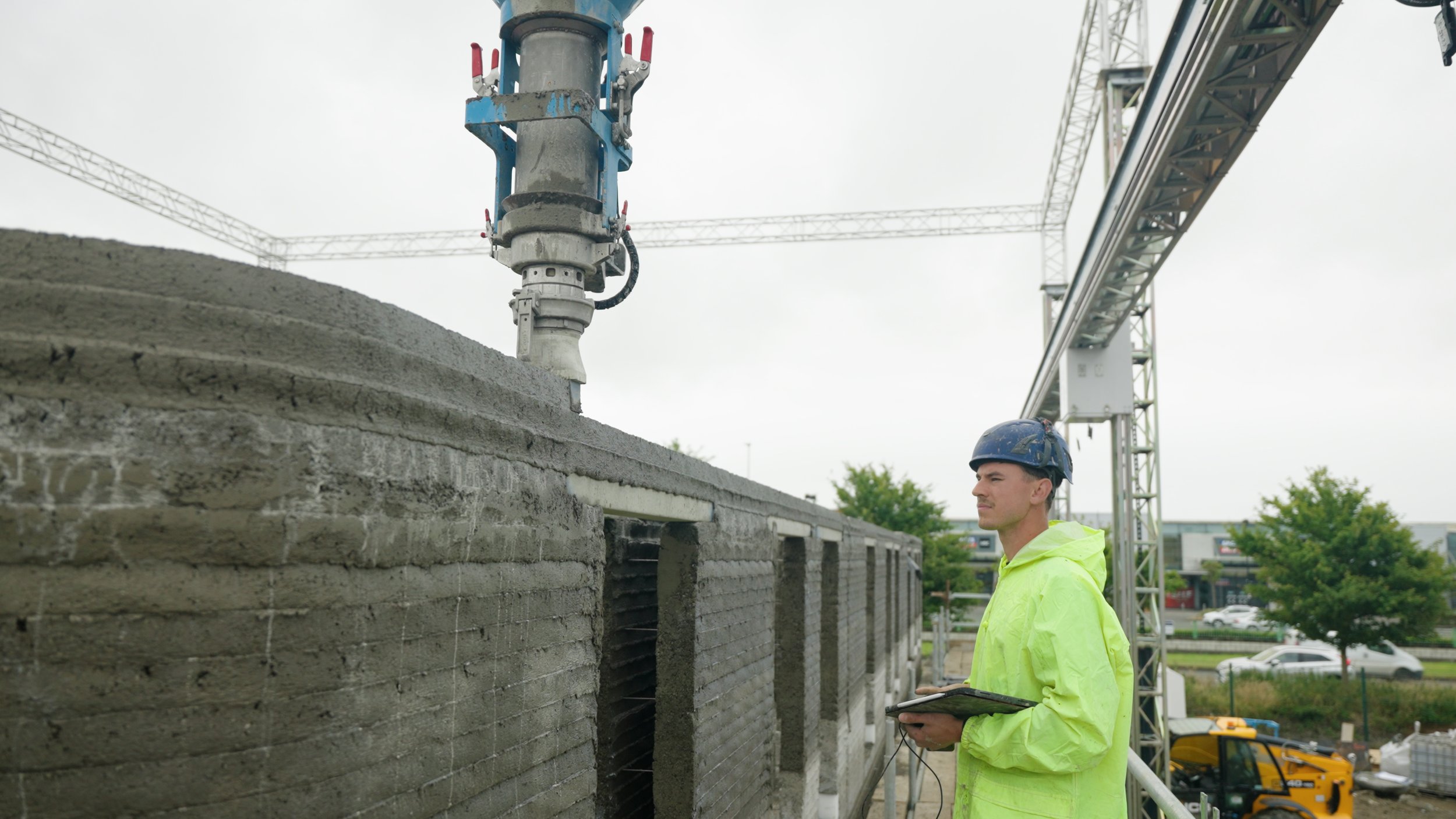
The load-bearing wall system is designed to meet the Eurocode 6 masonry standard.
Walls at Grange Close have two 10cm-thick skins with a 150mm cavity in between. No reinforcement or columns were needed.
Some 90 cubic metres of C30/37-EN206-compliant concrete with a compression strength of 47 MPa were used.
The structure complies with the ISO/ASTM 52939:2023 standard for additive manufacturing, which Ireland has adopted.
HTL.tech director Justin Kinsella said the Cobod printer allowed the project “to establish new industry standards and offer an effective means to produce high-quality, sustainable housing at an accelerated rate”.
In October, HTL.tech won the Standards Innovation Award from the National Standards Authority of Ireland.